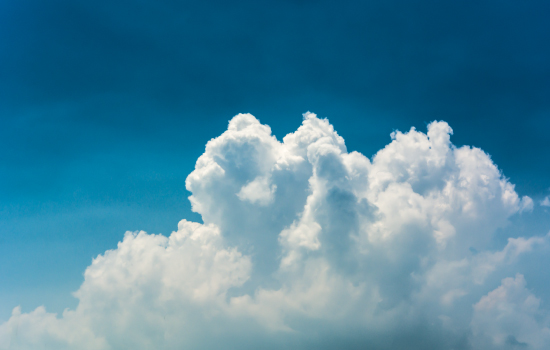
La desalinización se posicionó como una solución a la escasez de agua y como respuesta a un mejor uso del recurso hídrico en la minería, pero vino con un desafío: el del consumo energético y su eficiencia. Los cálculos que hacen desde la empresa Negawatt coinciden con los de Cochilco: cerca del 7% del consumo de energía eléctrica del sector está asociado a la desalinización, con 1,7 TWh/año, en un escenario donde se proyecta que el consumo de agua de mar se triplicará en un lapso de diez años.
“Si el consumo por m3 de agua desalada es de 3 kWh/m3, al que hay que agregar la impulsión hacia las faenas mineras, se podría indicar que cada m3 equivale a cerca de 12 kWh. Dado lo anterior se proyecta que el consumo de la desalación e impulsión podría llegar a ser del orden de los 5 TWh/ año en diez años, con lo que la desalación se proyectaría como el segundo mayor consumo de energía eléctrica entre los procesos mineros”, estima Juan Peñailillo, gerente general de Negawatt.
En Chile actualmente hay 24 plantas en operación que producen un total de 9.703 l/s, cinco plantas en construcción que aportarán 3.904 l/s adicionales, tres con resolución de calificación ambiental o con perspectivas de licitación que aportarían otros 3.136 l/s, y 35 proyectos de producción de agua de fuentes marítimas y residuales y de uso de agua de mar para la minería y la generación de energía eléctrica, según el último catastro de la Asociación Chilena de Desalación y Reúso (ACADES).
Rafael Palacios, vicepresidente ejecutivo de este gremio, explica que el consumo de energía promedio de una planta desaladora de agua de mar mediante la tecnología de ósmosis inversa es actualmente de 3 a 3,5 Kwh/ m3. Dice que en Chile, las plantas están funcionando en un promedio de 3,5 Kwh/m3, y que la de Nueva Atacama, en Caldera, es “la más eficiente y moderna”, ya que alcanza un consumo de 2,81 Kwh/m3. Para ponerlo en perspectiva da varios ejemplos: “Considerando que el consumo promedio de agua de una persona es de 100 litros por día, la energía eléctrica utilizada para abastecer de agua desalada a una familia de cuatro personas durante un día es equivalente al consumo eléctrico diario de un refrigerador, a 38 minutos de una secadora, a 40 minutos de un hervidor o a una hora de planchado”.
Los procesos más demandantes
Palacios explica que, justamente, los procesos más intensivos en energía de la desalación de agua de mar son el de ósmosis inversa, por una parte, y de transporte y elevación del agua producto, por otra.“La producción de agua desalada considera las etapas de captación, pretratamiento, ósmosis inversa y postratamiento, y la ósmosis inversa representa entre un 60% y un 70% del consumo total de energía de la producción de agua”, dice. Pero una vez producida, es necesario llevarla al lugar donde será utilizada, lo que en términos de consumo energético puede representar un total equivalente al de todo el ciclo de producción, si es que el agua es entregada a cortas distancias e igual cota, explica. Cuando el agua debe ser transportada y elevada a cotas sobre los 1.800 o 2.400 metros sobre el nivel del mar, el consumo de energía puede llegar a ser tres o cuatro veces más que el consumo total del ciclo de producción.
Palacios recuerda que todas las plantas que abastecen de agua de mar desalada a la minería están sujetas a la nueva ley de eficiencia energética. Sin embargo, remarca la existencia de desafíos como el transporte hídrico a los centros de consumo, que en el caso de la industria pueden estar ubicados a más de 4 mil metros de altura y a más de 150 kilómetros. “Por tanto es necesario avanzar en el diseño de infraestructura compartida que nos lleve a un sistema integrado de abastecimiento hídrico en Chile”, advierte.
Peñailillo acota que el principal desafío está en la elección correcta de los sistemas desde el inicio del proyecto, es decir, desde el diseño de la planta.
Pero la tecnología está siendo clave para mejorar la eficiencia energética en estos procesos y también reducir los costos, observa Gustavo Inostroza, Head of AI & Data Science en Wingsoft. Una de las soluciones que más se ha implementado en la industria, según ha observado, son los intercambiadores de presión, recuperadores de energía que reutilizan la del flujo de agua salada de rechazo y reducen el consumo energético hasta en un 60%.“Esta innovación mejora la eficiencia y disminuye los costos operativos, ofreciendo retornos atractivos para los inversionistas”, destaca. Las membranas avanzadas y la integración de energías renovables, especialmente la solar y eólica, también están causando impactos positivos, acota.
Para Peñailillo, la digitalización del control de los procesos también está definiendo el camino, específicamente con el uso de big data, altos niveles de sensorización y, potencialmente, inteligencia artificial.